Bretonstone - The First of Engineered Stone
- Breton USA
- Aug 12, 2019
- 10 min read
Updated: Sep 5, 2019

The Bretonstone success story is one of a dream come true and an integral part of Breton SpA’s 55 plus years of continued technological innovation.
In 1966, three years after Breton opened its doors, Marcello Toncelli, the founder of Breton, saw his first engineered stone plant be installed.
He knew there was a future in industrial stone plants that could mass produce quartz slabs in many different configurations.
There are various designs, colors, materials and structures that can be engineered at the press of a button.
Because of his vision, we can appreciate the beautiful engineered stone counter tops that are heavily sought after by home owners, fabrication shops and interior designers.
The birth of engineered stone starts here.
BOLD VISION

Above all else, this story is about the man who established the company, Marcello Toncelli.
It is also about all the people who saw his vision, believed in what he was doing, and helped him make the Bretonstone® dream come true.
Brevetti Toncelli was established in 1963 at Castello di Godego in the province of Treviso.
The name soon changed to Bre-Ton, and then to what it is known as today: Breton
However, soon after the company soon began developing technologies and plants for the production of what was once commonly called “agglomerate.”
This material is made of stone fragments bonded together by resins, known today as Engineered Stone.
DRIVEN BY INNOVATION
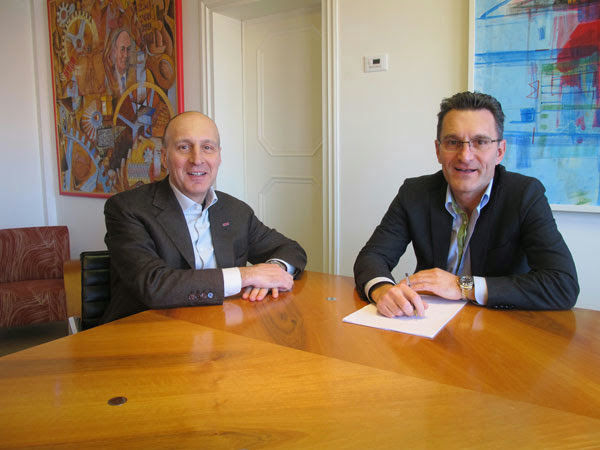
Breton is now run by Mr. Toncelli's sons, Luca and Dario Toncelli.
To this day, they are prolonging their father’s dream of being a world renown company who has made research its motto: Driven by Innovation.
Breton employs nearly 1,000 people in total with four Veneto production plants, several foreign-based sister companies, including Breton USA, and has an annual turnover of over 200 million euros.
The company's closest collaborators said Marcello Toncelli was always one step ahead of everyone else.
Sometimes, even so far ahead he might have seemed rash at times.
But he had a dream and the insight and the passion to make his dream come true. Breton is now at the hands of Luca and Dario continuing to drive innovation and uphold their father’s dream and vision.
BIRTH OF ENGINEERED STONE

Originally, Bretonstone was engineered stone blocks made up of polyester resins and marble fragments. These materials were hand poured into 30 x 50cm and 300 x 125cm molds to be compacted. After the blocks were formed, CNC machines then cut them into slabs.
The slabs cut from bigger engineered stone blocks had a Palladian appearance. Andrea Palladio was an Italian architect from the 16th century who is widely considered one of the most influential architects ever.
Fast forward to the early 1970's where a new innovative idea was given to the engineered stone process to produce a different kind of look.
Toncelli thought using smaller aggregates would give the slabs a granite-like appearance and would no longer require cutting engineered stone blocks.
And so, in 1975 his dream of Bretonstone came to fruition, followed by engineering new technologies and inventions.
TRIAL AND ERROR

At first, there were problems that took a long time to resolve, some of which create fondly remembered stories.
Since the first engineered stone slabs were subject to porosity, air bubbles were getting trapped in the resins.
So, Marcello Toncelli came up with the memorable “hot water bottle” solution.
He put engineered stone resins in a hot water bottle, screwed it tight, and then beat the bottle with a hammer on a block of wood.
This made the mix more compact and then put the lot in the oven to cure, and when the rubber was peeled back, the first Bretonstone tile was born.
Now all we had to do was come up with a way to use this method on a larger scale for mass production.
However, large slabs still tended to curve while they cured.
SUCCESS AT LAST
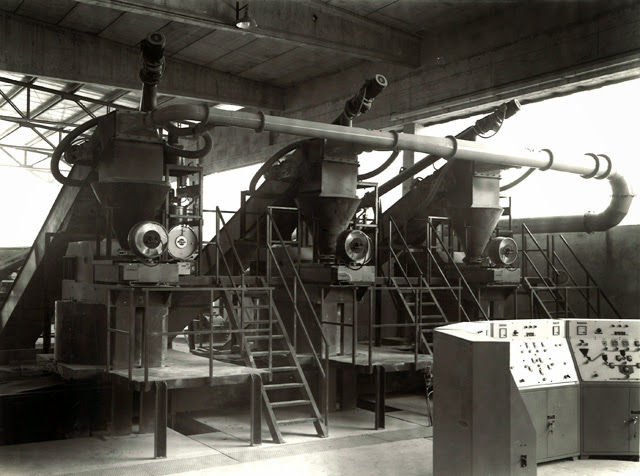
Finally, after years or product development, experimentation and research, the first Bretonstone plant was sold in 1979 to a ceramic based company in Tunisia. The trick was creating a vibro-compression vacuum technology that mixes a minimum polyester resin content to create the perfect results. It was the exact technical solution we were looking for. Soon after the first plant was sold, more followed quickly after. These engineered stone plants found their way into other countries, such as Venezula, Singapore, The United States of America, Spain and other Italian regions. By discovering machines needed for mass producing large slabs, creating an engineered stone product free of porosity and the particle size effect of the aggregates was emphasized: success at last!
BELIEVING IN INNOVATION

It took some time for the market to realize its potential, which required many showroom installations. Architects did not know how the resin would behave and react to its elements overtime.
They thought that the exposure to the sun and atmospheric agents would hinder the ability for this product to take off.
There were also fears about it easily be scratched and scuffed. The concerns of these architects derived from the thought that quartz is not as strong as granite and other natural stones.
A great deal of skepticism surrounded the launch of Bretonstone. 56 years later, Marcello Toncelli and his team at Breton proved them wrong. This was a result of their belief in a product created with the most innovative technologies of their time.
Breton never lost faith in their vision and the product, which is reaffirmed today as engineered stone counter tops are becoming more popular than ever.
RELENTLESS PURSUIT OF EXCELLENCE

The first Bretonstone slabs were characterized by a property that was considered a limit by the market.
Despite the fact that they looked like granite, the mix of polyester resin and marble aggregates were physically more similar to marble. However, there was a slight problem. These Bretonstone slabs were not as hard as granite counter tops.
In order to obtain the same hardness as granite, we had to find new materials to mix into the engineered stone resin compound.
Breton’s Research & Development team decided that using siliceous stone and quartz was the best way to accomplish this.
Obtaining the same hardness as granite was acquired with this new mixture but it required more work.
INSTALLATIONS AND PROGRESS

In the late 1970's, Breton engineered a machine fitted with heads and oscillating sectors for polishing hard stone surfaces in production lines within Bretonstone plants to fabricate the best possible product for consumers.
One of these machines was the ground-breaking Levibreton KG. It became an instant success all over the world in the early 1980's.
This led to the idea of producing Bretonstone with harder aggregates. In 1982, Breton supplied Saro of Trento with a plant to produce 125 x 125cm Bretonstone slabs made with granular porphyry. Two years later, in 1984, a similar plant was supplied to the UK-based company Marble Work, to produce slabs made of silica sand. The first Bretonstone plants that used silica sand and ground quartz were purchased from Caeserstone and Cosentino.
GAINING TRACTION

At this point, Bretonstone was now just as beautiful as granite, but it offered way better performances than it.
Breton made engineered stone more resistant and non-absorbent, as these slabs are non-porous.
Soon after, all Bretonstone manufacturers switched to silica sand and quartz-based mixes.
It was the natural evolution of processing engineered stone countertops. In 1987, the Israeli company – Caesarstone©, bought the first Bretonstone plant utilizing the newest technologies for producing the biggest slabs yet: 125x308cm. Cosentino© was the next engineered stone manufacturer to use the Bretonstone plant technology for producing slabs of this size.
LIMITLESS PARTNERSHIPS

Marble Work is living proof that innovation knows no limits. After converting to the new resin mix with harder aggregates, fantastic results were obtained at their United Kingdom plant.
They are now quoted on the New York NASDAQ stock market, and the owner of 4 plants, soon to become 6.
The installation of the Bretonstone plant was a great success for Cosentino also. By investing in the most innovative technology and putting quality first, it positioned them as an industry leader in their market.
Originally, they bought a plant to use waste from their Macael white marble quarry in 1989 and later switched production to quartz with Silestone.
This resulted in exponential growth for them.
Along with a successful and effective marketing policy developed in the North American market, a first plant was soon followed by a second, a third, the forth, and the company now owns 11 Breton engineered stone plants.
Cosentino is the biggest producer of Bretonstone quartz in the world.
JUMBO SLABS
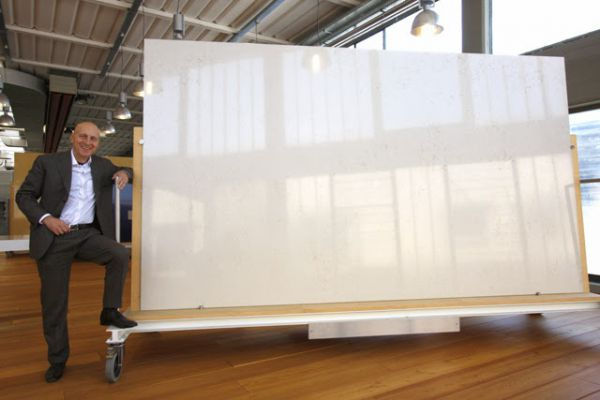
As with all things, the demand of engineered stone and other quartz-based surfaces continues to change over time.
Breton’s ability to adapt to market needs and execute market research lets our engineers keep innovating new technologies for all your needs.
Bretonstone slabs have come a long way since they first came to fruition, in the shape of blocks. With that, the size of Bretonstone slabs have evolved with time. They have increased from 125 to 144 and then 166cm.
BUT. That still was not enough.
We now offer plants created with truly the most innovative technology available today to produce Bretonstone jumbo slabs: 212 x 367cm.
Aesthetically amazing slabs with quality such as these behold an infinite number of possible configurations and uses.
BRETONSTONE BLOCKS
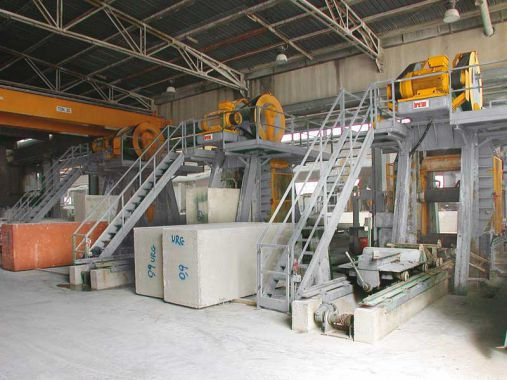
Breton has also patented other technologies and systems for manufacturing engineered stone blocks.
These are not your ordinary blocks. They are large, composite stone structures made of natural limestone aggregates and polyester resins.
Engineered stone plants that rely on and manufacture Bretonstone blocks use similar technology as the slabs. Like Marcello Toncelli’s original idea, the vacuum vibrocompression presses the stone aggregates, mineral fillers and organic binders into 308x125x88 cm or 308x140x88cm blocks.
The blocks then either meet a wire cutter to be cut into slabs to size or can be kept as blocks for different designs.
All said and done, the stone aggregates constitute 96% of the weight of the finished product
The production capacity, depending on the model and composition of the plant varies from 1,500 to 8,000 m2 per working day.
BRETONTERASTONE AVANTGARDE
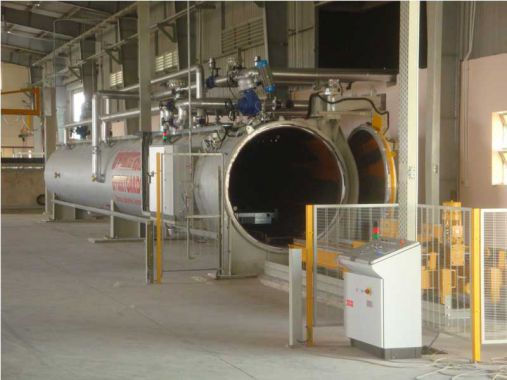
Bretonterastone Avantgarde is made of thin, single-layered tiles and slabs.
Avantgarde’s recipe for beautiful surfaces uses siliceous aggregates, such as quartz and granite, and is then connected with a highly reactive adhesive Portland cement paste.
The production technology that creates this Avantgarde engineered stone has drastically improved the technical characteristics, compared to the original Bretonterastone Classic.
Its exceptional characteristics means made an improvement of the traditional terrazzo tiles.
Avantgarde now features higher mechanical resistance, greater resistance to stains and chemical agents, greater dimensional stability, higher resistance to freezing, free from carbonation, efflorescence and alkali/silica reaction phenomena.
Since it is made of fine siliceous grains, Avantgarde is ideal for designing modern, trendy and high-performance surfaces with a uniform color tone.
BRETONSTONE CEMENT
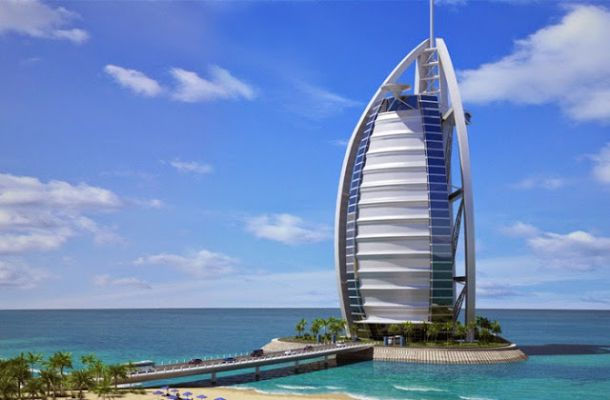
Bretonstone slabs are superior in the field of cement based-products for architecture from their exquisite aesthetics and countless colors.
Characteristics of Bretonstone Cement include low porosity resulting in low water absorption, higher resistances to frost/thaw cycles, flexing, wear and tear, UV rays and incombustibility.
These features make Bretonstone Cement a formidable product with the most uses in modern construction and furniture.
Because of their aesthetics, sizes and reduced thickness, this exceptional material is ideal for external and internal coverings, making it a cost-effective way to cover entire buildings.
Coupling Bretonstone Cement panels with supporting metal structures can designed different in various ways according to the designers and the building being worked on.
THE LOOK

Bretonstone has also evolved over the years. When engineered stone was first produced, it closely resembled granite the most.
After that, Breton began producing different color slabs. This of course was followed by veined engineered stone that resembles naturally veined marble.
The next Bretonstone slab style captured the essence of exotic Brazilian granites, such as Cambria's surfaces.
Each manufacturer has added their own personal touch to the aesthetic quality of engineered stone slabs.
Some of these exquisite touches include colored glass inserts, crystals, mirror fragments, semi-precious stones and brass filings to make the slabs speckle with gold.
Through hard work, dedication and persistence, Bretonstone has transformed into a product of prestige.
It was already a product of quality but now it is more beautiful than ever.
MULTIPLE USES

Today, a designer who wishes to create something special, to innovative at the highest quality will have no limits with Bretonstone slabs.
It is an elegant material with an added bonus of it being proven with time, a tradition like no other.
Bretonstone is the bridge between the past and what is to come! This material can be found in airports, shopping centers, on sky scrapers, exquisite hotels and more.
It has been used in many airports, such as Dubai, London Heathrow and Amsterdam to name only a few.
Bretonstone is also very popular as flooring surfaces in large scale quantities.
Shopping centers, malls, business lobbies and other similar places use it to obtain a natural stone-like appearance without having to spend as much money on it.
BRETONSTONE IN UNEXPECTED PLACES

Giorgio Armani in New York, Prada in Dubai, Fendi, Ferrè, Diesel, Swatch, Montblanc and others all rely on the attractiveness and durability of Bretonstone to represent their stores.
The Gallerie center in Lafayette, Sunset Mall in Dubai, Buji Al Arab hotel in Dubai, schools, hospitals, residential complexes, churches.
Mosques from Paris to the U.S. also use Bretonstone slabs.
Countries from the Arabian States to China, Malaysia, Singapore, Russia, Senegal, Brazil and Australia all find the value in this technology and use it.
There is a little bit of Italy all throughout the world, a little bit of the person who invented it, believed in it, and distributed this innovative Italian material, which lets architects’ dreams come true.
A WORLDWIDE REALITY

The phenomenon of our engineered stone technologies is felt all around the globe as its developed over the years.
Today there are approximately 60 engineered stone plants operating globally. This is great for Breton but even better for more people.
What really stands out though is the exponential number of jobs Bretonstone has created and continues to create all over the world.
When Breton installs an engineered stone plant, a few things happen: construction crews, resellers, slab designers, operators, distributor, fabricators and interior designers all find work because of it.
Bretonstone has created work for tens of thousands of people all over the world and produces over 20,000,000 m2 of slabs per year.
Most people have likely admired and appreciated slabs produced by Bretonstone plants without even knowing what the material is, often times simply called “Quartz.”
GOING FORWARD

Bretonstone is a totally eco-friendly green product, including the production process and finished product.
Today we are greener than ever, as we use Biolenica® resins made by using vegetable oils obtained from renewable sources.
Bretonstone is one big family with many trademarks that will keep the technology alive.
Every company producing Bretonstone has helped make the name something special, leaving their respective names on the market as an original.
Some of Breton’s clients that are using its technology for producing engineered stone slabs include Stone Italiana, Santa Margherita, Caesarstone, Lapitec, Technistone, Cosentino, Cambria, Seieffe, Quarella, Privilege, Silicalia, Hanwha, AKG, DuPont, Vicostone, Diresco, Falat, ZKM, Pokarna, Quartzforms, LG, Belenco and Daelim.

Being a global leader in engineered stone with proud Italian heritage, we never believed in delocalization and made the creativity and professional qualities found in Italy the cornerstones of our company.
Come learn more about Bretonstone at BOOTH 3872 during Coverings 2019.
This trade show is the perfect opportunity to discover why Bretonstone slabs and coverings are the best option for your business.
Please email machinesales@bretonusa.com or call (941) 960-8753 today if you have any immediate questions about Bretonstone, our bridge saws, CNC routers or edge polishing machines for the stone industry!
Comments