COMBICUT DJ/NC 550
- Breton USA
- Aug 12, 2019
- 7 min read
Updated: Sep 5, 2019
Revolutionizing the stone industry with the first ever combination bridge saw & water jet.
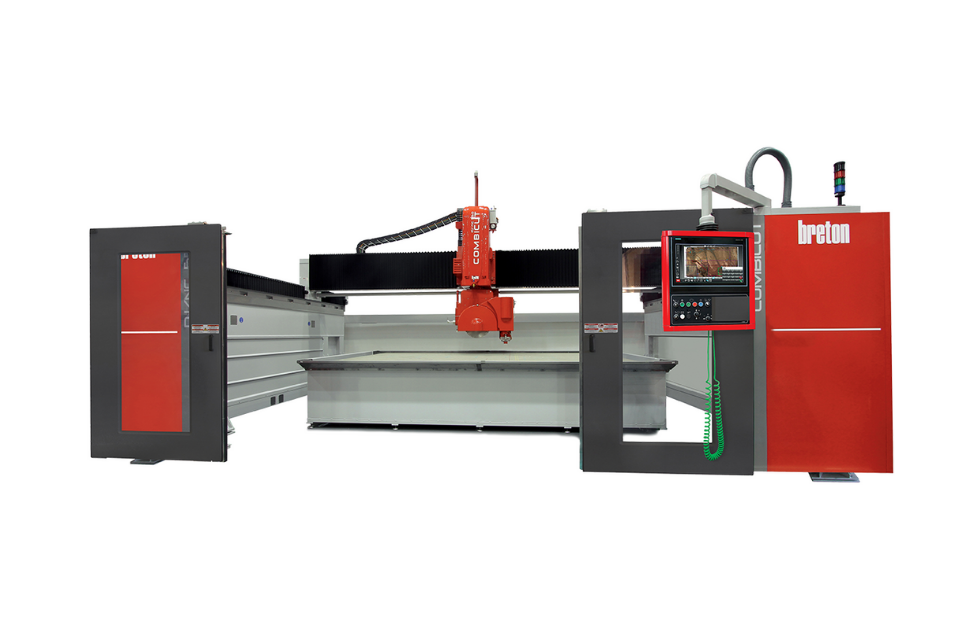
Breton Pioneers the Sawjet
In 2005, Breton introduced the Combicut, the first sawjet the stone industry has ever seen. To this day, it is a recognized industry-leader for accuracy, ease-of-use, efficiency, ergonomics, optimizing production and SAFETY.
Renowned for its precision and durability, this interpolated 5-axis sawjet has a rotating head for executing complex rectilinear, curvilinear and inclined cuts, even on materials that trouble the most advanced diamond blades and experienced CNC operators.
Once the CNC operator programs the computer numerical commands for the job, the Combicut utilizes and alternates cutting with the blade and waterjet.
With this technology, there is no need to move the slab and work pieces, thus optimizing cuts and minimizing wasted material.
Bridge saw + Waterjet = Sawjet
Sawjets are two-in-one machines engineered to perform several functions that usually require two different machines.
Regardless of the task at hand, a sawjet provides the latest and best innovative technology for cutting slabs of various materials in the stone industry.
Sawjets ensure that fabricators get the most accurate cuts, optimize production, and can cut surfaces faster than any other solution on the market at the lowest cost with the highest quality.
They provide unrivaled flexibility, being able to cut any material with zero breakages, and produce inclined cuts that can be performed with the highest precision with minimal off-cuts.
Pursuit of Perfection
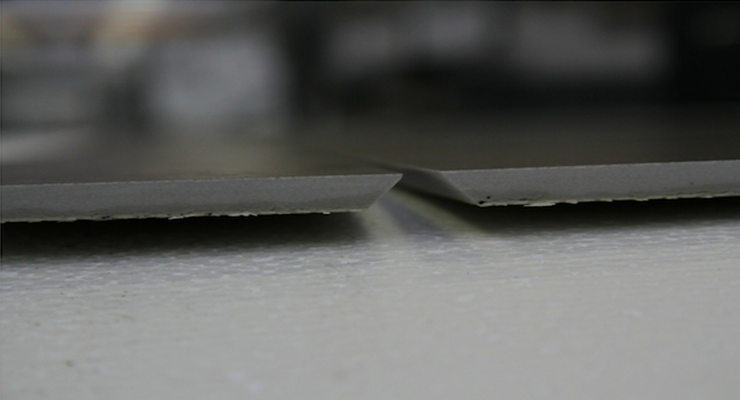
Since 1963, Breton’s research and development team has been engineering cutting-edge technology for fabrication shops to optimize their cutting operations at the highest level.
Sawjet technology provides fabrication shops cascading benefits.
Sawjets save room, optimize material usage, and have a low investment price with a high ROI since jobs can be executed with only one machine.
The capabilities of sawjets are ideal for CNC operators that regularly carry out complex cuts.
Stainless Steel Tank

The Combicut’s stainless steel tank has a long-life cycle because its ability to minimize wear and tear on the worktop. The slab rests on a stainless-steel table, consisting of bent, galvanized steel “consumption blades,” which are coated with a patented rubber profile to support the slab.
The rubber profiles are separate from the steel blades and are the only thing that the diamond blade/waterjet cuts through.
This enables clean cuts on the slab during the entire operation. These profiles are replaceable and less expensive than disposable worktops made of plywood and other materials.
The worktop slats eliminate the need to store and maintain underlayment boards.
Automatic Worktop Exchange
The Combicut comes standard with a fixed worktop, stainless steel tank, and consumption blades to support the slab as it is cut. However, upon request, this sawjet can be installed with an automatic worktop exchange system.
It automatically carries the worktop carrying a new uncut slab and exchanges it with the already cut slab.
While the current slab is being cut, the CNC operator can program the cutting scheme for the new slab outside of the machine prior to the exchange.
This feature drastically reduces downtime at the end of each cutting cycle and improves productivity.
Safety
Operating a bridge saw is the safest way to fabricate in the stone industry. This sawjet’s sliding doors have large, transparent windows guaranteeing the failsafe of the machine. They create quieter operations and protect CNC operators by preventing diamond blade teeth, material fragments and other projectiles from reaching them.
However, they can still monitor the operation as the sawjet carries out the commands thanks to the clear windows.
The safety doors comply with CE Accident Prevention Regulations and with the UL/CSA North American Standards. The thermoformed ABS doors are made with sound absorbing foam, creating a better work environment for the operator by limiting their exposure to noise, protecting their hearing, and helping them hear others yell if an emergency arises.
Cutting Unit

This sawjet’s spindle houses an unrivaled cutting unit that has not been matched by any other manufacturer in the industry.
It consists of a diamond saw blade, high-pressure waterjet, slab thickness probe, and a laser tracer to guarantee accuracy during all cutting operations. CNC operators can change blades easier than ever with the Combicut.
There is only one screw on the blade’s protective barrier, helping jobs get done quicker, especially for projects with sintered/ceramic materials that require a lot of blade changeover.
The Combicut’s cutting unit offers the stone industry something nobody else can: perfect execution of 45° miters.
Cutting Inverter
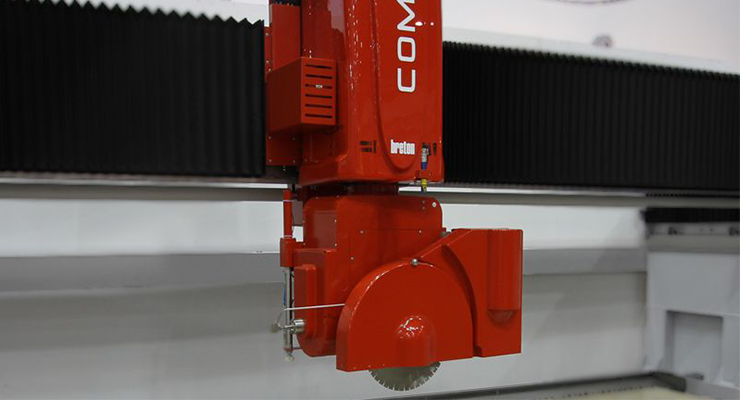
A cutting inverter comes standard on every Combicut.
The inverter is material specific, providing automatic and continuous variations in the diamond blade’s RPMs, according to the programmed commands and the material being cut.
This feature is beneficial for CNC operators that saw different materials, especially ceramic and quartz.
KMT

Breton only partners industry-leading companies, like KMT Waterjet Systems.
With this collaboration, Breton and KMT engineered the best sawjet possible, creating the solution with the most uses.
Cutting ceramics and sintered materials with this sawjet is easier than ever and stress-free with the KMT Waterjet partnership. The KMT group directly provides the after sale technical service (both under warranty and post-warranty) through its network of service centers.
In 2016, Breton USA became an exclusive agent for parts and service for KMT Waterjet Systems, allowing our technicians to address the needs of your sawjet quicker.
Intensifier

Like the diamond blade’s inverter for automatically fluctuating RPMs, the Combicut comes with an intensifier for the waterjet.
It automatically and continuously compensates the natural taper of the pressure on the waterjet’s head for fluctuations in slab height, creating more precise cutting operations.
This allows CNC operators to fluctuate the pressure for various slab thicknesses and materials.
This feature ensures that you will get a perfect cut every time, miters included.
5th Axis
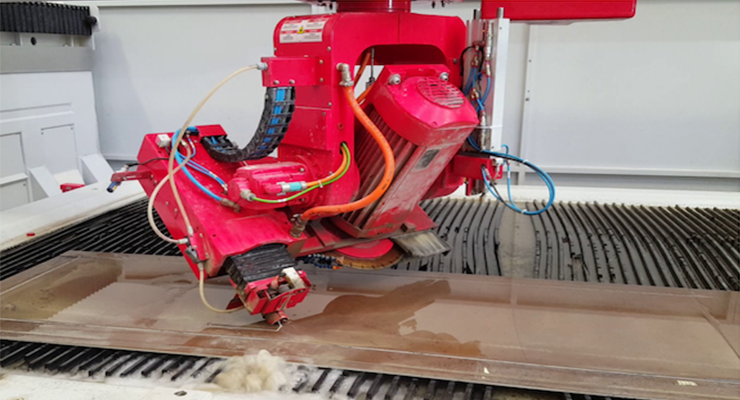
CNC operators can incline the diamond blade and waterjet to perform perfect 45° cuts.
This interpolation process is required for executing rabbets and performing 90° changes of direction without interruption, by incorporating all five axes simultaneously, using either the diamond blade or waterjet.
The sawjet rotates ± 190 ° around its 4th axis, providing unparalleled precision and cutting speed for complex rectilinear and curvilinear cuts. It is programmable for inclination cutting between 0° to 55° on the 5th axis. This advanced technology produces customized shapes, laminations, inlays, medallions, miters and mosaics.
All five axes are driven by Siemens brushless motors.
Fixed Camera

This sawjet can be supplied with a digital camera system to capture an image of the slab prior to cutting.
After a photo of the slab is taken, it is displayed on the Multitouch screen for the operator to manipulate and optimize material usage.
The CNC operator can also highlight defects and the perimeter on the slab.
The Combicut then automatically inserts the shapes to be cut inside of the working area, optimizing the exploitation of the surface.
MultiTouch
The Combicut is equipped with the latest generation Siemens Sinumerik 840D-SL, a computer numerical control (CNC) digitally controlled PC architecture with an Intel processor and Windows XP operating system.
Being swivel mounted, the Multitouch’s control panel is easily adjustable and comes with a 19-inch color touchscreen monitor, USB port, keyboard and a joystick for manually and intuitively moving the various axis.
The Multitouch’s operation and management software are simple and user-friendly.
MultiTouch Tools
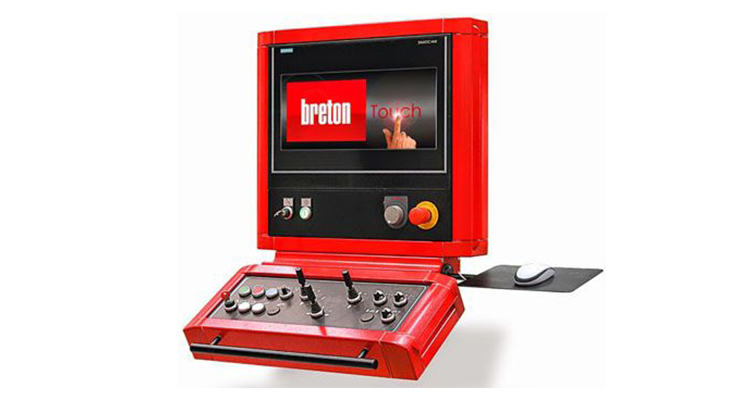
Slab editor: controls the digital camera installed on the machine, acquiring the entire slab with single-shot capture, letting CNC operators draw and highlight on the slab to be cut
Cut scheme: arranges the cutting scheme and automatically nests pieces on the screen, which can be moved, rotated or coupled with other pieces with its automatic snap feature
Cut move editor: calculates the cutting sequence and different handling operations needed for executing work orders
Shape Editor: makes it possible to draw on the slab with just the touch of a finger
Slab selector: manages the slab database
DB Orders: manages the order database
Nesting system: manages the automatic nesting of imported DXF files
Portable Remote

The axis, handwheel and emergency stop controls are easily manipulated and accessible from the portable remote panel.
This panel makes leaving the Multitouch screen during operations a non-issue.
With this portable remote, a CNC operator can closely monitor operations directly on the slab while the sawjet executes work orders and correct the execution of particularly delicate operations if needed.
A Breton sawjet can efficiently improve the ergonomics of your fabrication shop. This is only one of the solutions engineered with the operator in mind.
Slab Thickness Probe

In order to achieve second-to-none cuts, the CNC unit must know the exact measurements of the slab.
What is Breton’s solution?
Attach a slab thickness probe on the sawjet’s cutting head.
At the beginning and end of the cutting process, it compensates any possible variations of thickness to give you more accurate cuts.
It is especially helpful when measuring for v-cuts (inclinations of 45°).
Miterwave
Often, if not almost always, ceramic and sintered materials are not perfectly flat or planar, creating tensions, bends and inaccurate machining calibrations.
Breton presents Miterwave, a hardware and software package for executing perfect 45° miters cuts on uneven surfaces. Miterwave automatically measures and corrects the cutting trajectories by interpolating them continuously with the slab surface for virtually perfect results.
The Miterwave laser measures the exact slab height then continually and automatically corrects the cutting patterns to obtain consistently perfect folded edges. As a result, very little adjustment is needed at the time of adhesive bonding.
Miterboard

Miterboard is a user-friendly application dedicated to the creation of inclined surfaces using the sawjet’s water cutting feature.
It makes continuous inclined cuts at various angles out of a slab and then bonds it to the same slab later.
It is faster and more cost effective because milling inclined surfaces is no longer required, only the polishing stage is needed.
The finished result has the same color as the rest of the kitchen surfaces because it is made of the same material.
For through-body veined materials, the veining on slabs continues through the edge and inclined surface. The process takes around twenty minutes to complete.
Software
The compatible software for this sawjet takes CNC operators’ experiences with Breton to another level.
XpressTOP, the most advanced smart software suite on the market today for managing the entire counter top production cycle.
DigiHub, the easiest way to digitize CNC manuals, track real-time machine data, automatically supervise production lines, get reports, and gain access remotely while monitoring on a PC or any smart device.
Sentinel, a networked software solution that automatically gathers and processes manufacturing data in real-time. It helps owners, production managers, floor supervisors and accounting staff monitor and analyze machine production and efficiency both on site and remotely.

There is no better way to fulfill Industry 4.0’s rigorous standards than with an industry-leading sawjet to supercharge production while boosting accuracy, efficiency and slab optimization.
This two-in-one sawjet brings the stone industry the most competitive solution for doing more with less. It remains unrivaled for a reason.
If you are ready to partner with Breton USA for your technology needs or want to learn more about this machine, contact us today.
Call (941) 960-8753 or email MachineSales@BretonUSA.com now!
The Combicut and Genya 600 will be at The International Surface Event at the Mandalay Bay Convention Center in Las Vegas, Nevada.
Start planning your trip now if you are attending Coverings 2019 and schedule a visit to BOOTH 3872 from April 9 - 12 to see this sawjet in action.
Breton USA’s engineers and salesmen will be present to answer any questions you can throw at them and show you how these machines produce perfect miters. We cannot wait to see you there!
Commentaires